Appliance industry demand:
The home appliance industry currently has a fast production cycle, a large number of suppliers, and frequent congestion and waiting for vehicles entering the factory. The production line will be suspended due to the logistics of key parts not entering the factory. A series of transfer operations from raw material warehouses to production lines are mainly manual operations, facing a large number of labor, time and effort, low logistics efficiency, difficulty in finding materials, and inaccurate inventory information; home appliances Industry competition is becoming increasingly fierce, presenting high requirements such as multiple varieties, multiple batches, short delivery time, low cost, flexible manufacturing, rapid response, energy saving and emission reduction.
sygole Intelligent Logistics Solution:
sygole's production, distribution, logistics and asset management in the household appliance production industry have formed a complete set of system solutions to achieve the purpose of eliminating intermediate links, transparent and controllable data information, and saving people to improve efficiency. Our solution has played a huge economic benefit in many leading home appliance companies.
Application link:
1 RFID intelligent production line assembly:
² Customer pain points: mixed production, islands of line equipment information and quality control improvement
² Solution: Through RFID collection technology, complete the unmanned, automatic and real-time identification of single-grade products on the production line, use the real-time collected product information to complete the error prevention of mixed-flow production materials, real-time push of process guidance, and automatic diversion of defective products offline , Automatic generation of quality reports, product traceability management, mixed flow line change alarm, automatic equipment docking, etc.
² Value benefit: 60% of the time for skilled operation of new employees, to ensure the accuracy of the assembly process; to achieve error-free assembly of materials; docking automatic processing / testing equipment, automatic configuration / calling of procedures / parameters; automatic docking of quality data, accurate traceability; realization Abnormal products are automatically diverted and repaired off the assembly line; production progress is visualized and monitored in real time.
2 RFID tool management system:
² Customer pain points: The life of the tool cannot be tracked in the oil, metal, and high-temperature environments of the processing workshop, which is easy to cause huge losses in the short-term or failure of the tool during production.
² Solution: By installing RFID tags on the tool holder, using the tool combination operation, the tool holder and the tool are associated in the tool management system, so that the tool information is managed by RFID; by installing the RFID reader in the CNC machining center , Through the transformation of the machine tool PLC, NC and HMI, automatic tool parameter transmission, tool loading tool verification and tool life management control; by judging and fixed-point identification of the product carrier (ie the material tray) at the processing station, matching the production line The robot and the transmission mechanism jointly realize the automation and unmanned production process.
² Value benefit: There is no manual intervention in the data transmission process, and the error rate is greatly reduced; real-time monitoring and updating of tool life information, effectively extending tool life; automatic tool information recognition, transparent data management is more detailed; product mixed production, distribution and manufacturing processes No one intervenes; the rate of defective machining caused by cutting tools is reduced by 50%, the machine tool utilization rate is increased by 8%, and the tool life is increased by 20%.
3 Logistics vehicle guidance and unloading:
² Customer pain points: fast production cycle, large number of suppliers, and frequent congestion and waiting for vehicles entering the factory. The production line will be stopped due to the logistics of key parts not entering the factory.
² Solution: By distributing active RFID electronic tags to supplier vehicles, it is used to correlate vehicle delivery information (material type, quantity and unloading position, etc.), as whether to allow supplier vehicles to enter the factory to unload and allocate unloading positions Basis: Configure an intelligent reservation terminal outside the factory area to quickly complete the unloading space reservation; at the same time configure the online reservation function of the web version, suppliers can access the web page through the external network to achieve online reservations to avoid the situation of early delivery or late delivery of the supplier Occurred; L ED screen and status indicator light are installed on the unloading position to complete real-time guidance on unloading, display of unused and busy status of unloading position and timely reminder of unloading overtime: at the same time, according to the individual needs of the enterprise and business process, customize and develop business The management system can be seamlessly connected with ERP, MES, WMS, etc.
² Value benefit: realize the functions of automatic release of delivery vehicles, automatic allocation and guidance of unloading positions, real-time monitoring of unloading position status, timely reminding of unloading overtime, etc .; the vehicle congestion rate at the factory entrance is reduced by 70%. The abnormal work hours caused by the lack of materials in time caused by the goods are reduced by 80%, the workload of the security personnel at the factory entrance is reduced by 5%, the original resource allocation work (such as forklifts) is saved by 50%, and the warehouse inventory is reduced by 15%.
4 Transparency of production line data information:
² Customer pain points: The competition in the home appliance industry is becoming increasingly fierce, presenting high requirements for multiple varieties, multiple batches, short delivery time, low cost, flexible manufacturing, rapid response, energy saving and emission reduction, which requires our production line to be transparent, controllable, smart and efficient.
² Solution: Through RFID collection technology, complete the unmanned, automatic and real-time identification of single-grade products on the production line, use the real-time collected product information to complete the error prevention of mixed-flow production materials, real-time push of process guidance, and automatic diversion of defective products offline , Automatic generation of quality reports, product traceability management, mixed flow line change alarm, automatic equipment docking, etc.
² Value gain: reduce the skilled operation time of new employees by 60% to ensure the accuracy of assembly process; realize error-free assembly of materials; docking automatic processing / testing equipment, automatic configuration / calling of procedures / parameters; automatic docking records and accurate traceability of quality data; realization Abnormal products are automatically diverted and repaired off the assembly line; production progress is visualized and monitored in real time.
Typical application cases:
The "RFID+" solution provided by Sigu has been widely used in many leading home appliance companies and has exerted tremendous economic benefits.
ü Typical case-A
Project Background:
A's current reminders, communications and other content are handled by phone and mail, as well as fines after the event. There is no early warning mechanism to warn suppliers to deliver as soon as possible; the vehicle will be released by the security guard at the door, which is likely to cause traffic jams and unloading resources at the door of the factory. Occupied by order, resulting in unbalanced unloading scheduling; in case of emergency delivery, you need to notify the supplier by phone, the door to let the security guard release and artificially allocate the unloading position, but this program has many communication links, the efficiency of accident avoidance is low, and it is easy to form a shutdown.
An Introduction:
After passing sygole research, provide the following solutions
● Distribution of active RFID electronic tags to supplier vehicles, used to correlate vehicle delivery information (material type, quantity and unloading position, etc.), as a basis for whether to allow supplier vehicles to enter the factory to unload and assign unloading positions; in the factory area Configure an intelligent reservation terminal outside to quickly complete the unloading space reservation; at the same time configure the online reservation function of the web version, the supplier can access the web page through the external network to achieve online reservation, to avoid the situation of early delivery or late delivery of the supplier;
● Install LED screen and status display light on the unloading position to complete real-time guidance on unloading, display of idle and busy status of unloading position and timely reminder of unloading overtime;
● At the same time, according to the company's individual needs and business processes, customized and self-developed business management system can be seamlessly connected with ERP, MES, WMS, etc.
Value gain:
Realize the functions of automatic release of delivery vehicles, automatic allocation and guidance of unloading positions, real-time monitoring of unloading positions, and timely reminders of unloading overtime at home appliance factory suppliers; vehicle congestion rate at the factory entrance is reduced by 70%, due to untimely delivery Abnormal work hours caused by lack of materials are reduced by 80%, the workload of security personnel at the factory door is reduced by 5%, the original resource allocation work (such as forklifts) is saved by 50%, and warehouse inventory is reduced by 15%.
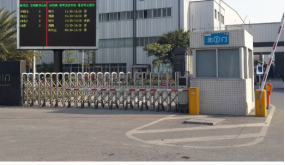
Supplier appointment information display
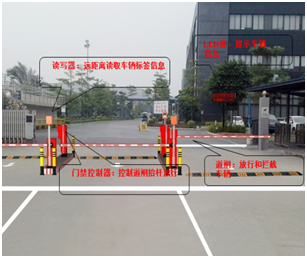
Automatic identification of entrances and exits of the plant
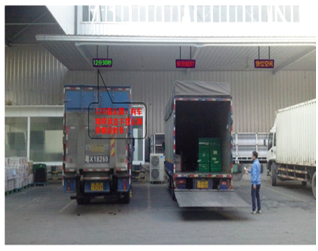
Path guidance for vehicle unloading position
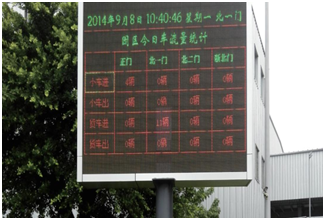
Real-time monitoring of unloadinginformation
ü Typical case-B
Project Background:
B's processing workshops rely on manual methods and paper barcode management tools. Paper barcodes are easily stained in oily environments, cannot reliably transfer parameters, and cannot achieve M2M communication. The tool life can only be judged by experience. Easily causes:
● Information is opaque, easy to waste, and rising costs;
● Long processing preparation time and low processing efficiency of CNC equipment;
● Lack of materials leads to suspension of production, delays in production, and high risk of delivery;
● Parameters cannot be effectively transferred, which may cause errors and affect product quality.
An Introduction:
● Install the RFID tag on the tool for identification and information reading and writing of the entire life cycle of the tool;
● Install a reader on the host machine of the CNC machine tool and other equipment as an information interaction interface between the RFID tag and the host machine control system;
● Using RFID tags as information carriers to realize the information interaction (M2M) between the tool and the host and between the host and the host, thereby reducing the processing assistance time of the host and realizing the prediction of the life of the auxiliary equipment.
Value gain:
Realize tool life management, increase life, effectively reduce processing equipment preparation time, increase machine tool utilization, reduce tool inventory by 20%, reduce tool cost by 10%, reduce preparation time by 15%, increase equipment efficiency by 10%, and shorten delivery time 10%, reducing the overall cost by more than 15%.

ü Typical Case-C
Project Background :
The manual code scanning mode consumes manpower: as each person needs to perform each code scanning operation and as the scale of production expands, the number of manpower that requires manual code scanning surges:
Low recognition rate of fixed scanning mode: The barcode recognition rate is low due to the gray layer and oil pollution at the production site, which cannot support the accurate operation of the MES system on the production line / assembly line information management.
An Introduction:
● Insert industrial RFID electronic tags on tooling boards / pallets / containers, and write production process information into electronic tags to replace paper barcodes, which has the advantages of oil resistance, reusability, and easy identification;
● Add RFID reading and writing equipment to meet the application of industrial environment on the production line / assembly line station, as a key equipment for data collection in MES system, to achieve information transmission.
Value gain:
To achieve multi-variety mixed flow assembly, process data is automatically collected, the data collection rate is increased to 99%, the manual barcode scanning time of each product is reduced by more than 90%, and the MES data accuracy rate is increased to 90%.
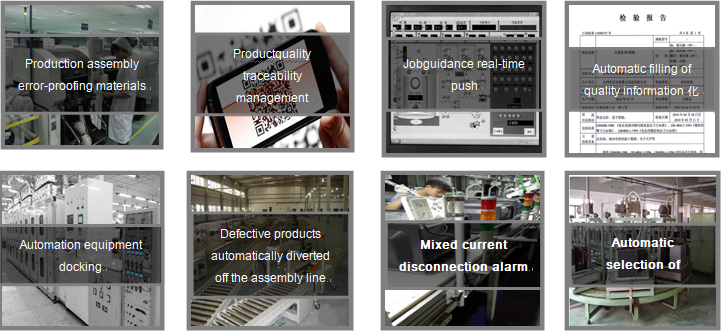