3C Industry needs:
In recent years, with the favorable policies, the improvement of related technologies and the market demand, the 3C industry has developed rapidly. Up to now, China's 3C market has enteredperiod of stable development. The 3C industry is the second largest market after the automotive industry. With the development of smart manufacturing, more and more IoT technologies are widely used in 3C enterprises. The construction of smart factories is an inevitable trend for the development of 3C enterprises. As the core of smart factory construction, smart production lines and smart equipment are the direction of 3C enterprises to focus on transformation.
Sygole solution:
With RFID automatic identification technology as the core, it provides solutions for 3C industry manufacturing plants' logistics intelligence, production line intelligence, and equipment intelligence.
Application link:
Logistics intelligence
² Industry characteristics: The material receipt and delivery turnover is large, there are many circulation positions on the site, and the logistics data is mainly recorded manually.
² Customer pain points: manual operation is tedious and error-prone, low efficiency, high investment in logistics equipment, insufficient utilization of logistics resources, and high management costs.
² Solution: By installing RFID tags on logistics turnover equipment and installing automatic identification equipment at each logistics node in the factory, real-time tracking of the logistics position of turnover equipment and materials in the factory can be achieved. Connect with WMS and other systems to realize real-time interaction of logistics data.
² Value benefit: Optimize logistics management, improve the turnover efficiency of materials and logistics appliances, realize the transparency of logistics information, reduce the cost of logistics resource input, and improve the overall management level.
Application link
Intelligent production line
² Industry characteristics: high automation level, fast beat, real-time data collection, strict quality traceability.
² Customer pain points: The data collection is mainly manual, and the real-time performance is poor; the information collected by each process data is difficult to integrate and error-prone, the quality traceability is difficult, and the production efficiency is difficult to meet the risk of line stoppage.
² Solution: Through RFID collection technology, complete unmanned, automatic, real-time identification of single-grade products on the production line, use real-time collected product information to complete error prevention of mixed-flow production materials, real-time push of process guidance, automatic diversion of defective products, offline Functions such as automatic generation of quality reports, product traceability management, mixed flow line change alarms, and automated equipment docking.
² Value benefit: The accuracy of each process is achieved, there is no error in the production and assembly of materials, the product quality and production efficiency are improved, and the risk of production stoppage is reduced.
Application link
Intelligent equipment
² Industry characteristics: The robot hashigh coverage rate, mainly manual adjustment, and manually record processing information.
² Customer pain points: manual adjustment is error-prone, robot processing information and product information cannot be interacted in real time, and product quality cannot be guaranteed.
² Solution: Through RFID collection technology, install automatic identification equipment near the robot to realize intelligent robot loading and unloading, automatically identify the material tray information, obtain processing parameters, and solve the problems of traditional manual parameter adjustment and low error efficiency.
² Value benefit: The product information is traceable and transparent, and the processing information is modified flexibly to improve product quality and production efficiency.
Typical Case-A
A is a domestic manufacturer of precision molds and structural parts in the field of consumer electronics. Since July 2015, Sygole, B and other units have cooperated to establish a localized smart factory for it. This is a "demonstration project of intelligent manufacturing of mobile terminal accessories". For the sub-projects of automation and flexible processing workshops, Sygole provides it with a smart sensing solution for production lines based on RFID technology. The core is to track and mark products throughout the process. The process includes thread feed, CNC feed and replacement. Through the position determination and fixed point identification of product carriers (ie material trays) in the processing station, materials, cleaning, unloading and other work are carried out, in cooperation with production line robots and conveyor mechanisms, to achieve an automated and unattended production process.
programme introduction:
The specific plan is as follows:
l Install RFID electronic tags as unique identifiers on each tray, and bind the processed products when online.
l Install RFID automatic recognition readers and writers at each station and shunt point of the automatic line body to automatically identify the material tray labels, realize automatic identification of processed products, and automatic selection of processing paths.
l Production data is collected and presented in real time, and processing information is transmitted to the MES system in real time
Project application:
The project uses more than 200 high-frequency readers independently developed and produced by Sigu, more than 1500 pallet labels, and a mature production data collection system.
² Increase in value:
Realize the intelligent production of multi-variety logistics chaos, increase production efficiency by 20%, and reduce product defect rate by 90%.
² Core advantages:
Sygole products are suitable for a variety of industrial complex environments, with large storage capacity of tags, repeated flashing and recycling, high recognition accuracy of the reader and 24 hours of continuous work.
Product application pictures:
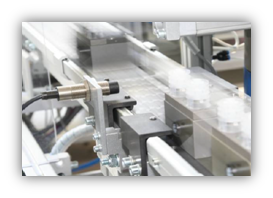
Installation drawing of the reader on the wire
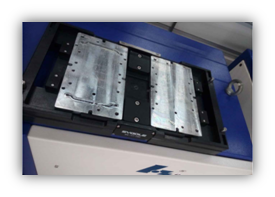
Installation drawing of the label on the material tray
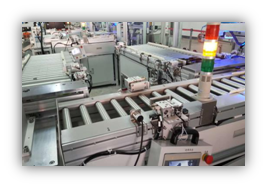
Overall hardware installation drawing of the thread feeding area